During the current fast-paced manufacturing ecosystem, the demand for quickness and effectiveness has reached new heights. As work to bring products to market at a quicker pace but ensuring high quality, innovative techniques are vital. An example of a technique that has earned significant momentum is rapid injection molding. This method doesn't only improve production rate and also maximizes resource use, making it a game-changer for contemporary factories.
Fast injection molding acts as a vital link in the product development pipeline, permitting manufacturers to create prototypes and production parts in a fraction of the time traditionally required. Employing innovative technology and materials, businesses can enhance their operations, reduce costs, and respond swiftly to market changes. With the increasing emphasis on efficiency, fast injection molding is proving to be the solution to realizing new levels of efficiency in the current competitive environment.
Engineering Overview
Rapid molding process is a innovative production process that greatly reduces the duration and materials needed to manufacture polymer parts. Differing from conventional molding techniques, which involves long manufacturing periods and costly dies, rapid injection molding utilizes advanced techniques to enhance the complete process. This methodology facilitates faster responses on prototypes and short production runs, which is ideal for sectors that require quickness and adaptability.
A key of the crucial methods that enable this process is the application of specific substances and high-tech equipment. High-performance thermoplastics and innovative mold design methodologies enhance production efficiency and produce detailed designs with precision. Furthermore, the implementation of automation and computer-aided design contributes to a efficient workflow, lessening mistakes and maximizing consistency across production batches.
Moreover, rapid injection molding plays a vital role in the adoption of JIT production techniques, allowing companies to react quickly to changing market demands. The capability to produce small quantities of premium parts enables manufacturers to hold minimal stock and cut overhead costs. As a result, businesses can remain agile in a rapid production environment, optimizing their operations and better serving their clients.
Benefits of Accelerated Injection Molding
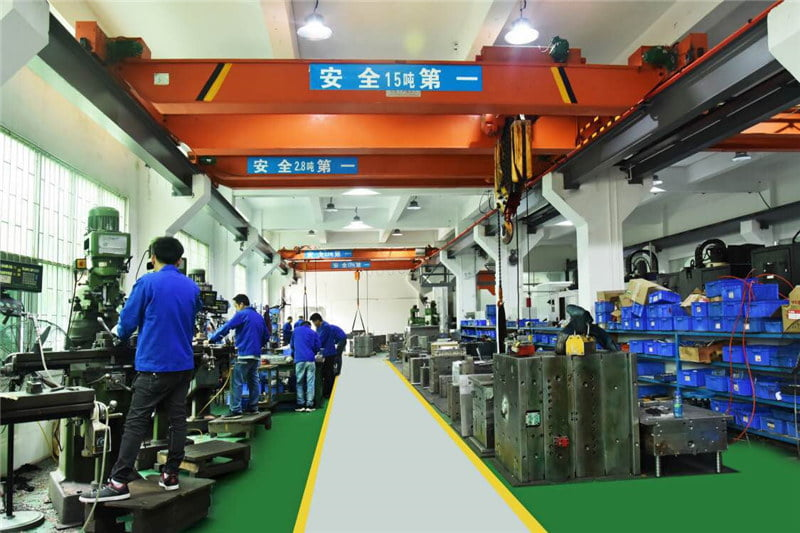
Quick injection molding delivers significant advantages that improve production effectiveness and minimize lead times in contemporary manufacturing environments. By leveraging innovative technologies, such as 3D printing for mold fabrication, businesses can quickly produce top-notch molds that satisfy exact specifications. This accelerated process permits manufacturers to respond swiftly to market demands, enabling them to deliver products to customers more quickly than traditional methods.
A further key benefit of accelerated injection molding is its affordability, especially for low to medium amount production runs. Conventional injection molding often requires high initial costs due to intricate mold designs and manufacturing processes. However, quick injection molding reduces these costs by allowing for easier mold designs and speedier setup times. As a result, companies can achieve significant savings while maintaining superior standards of quality and consistency in their products.
Furthermore, accelerated injection molding facilitates design revisions and improvements. With the capability to create molds quickly, manufacturers can test and refine their designs, allowing for greater advancement and adaptability in their product ranges. This cyclical approach not only boosts product quality but also motivates teams to explore new ideas, driving continuous improvement and operational efficiency within the factory.
Applications in Modern Manufacturing
Rapid molding has become progressively important in several fields of current manufacturing due to its capacity to simplify manufacturing processes. Industries such as automotive and home electronics receive substantially from this approach, as it permits the quick development of samples and short runs. In the fast-paced world of designing products, the capacity to quickly create elements means that businesses can evaluate their designs more efficiently and make necessary adjustments without having the long delays associated with conventional molding techniques.
Another notable implementation of this technology is in the medical device industry. The exactness and quickness offered by this technique allow manufacturers to make complex pieces that meet strict compliance requirements. As healthcare technology advances, the demand for quick prototyping and flexible manufacturing becomes critical. Fast injection molding facilitates the manufacture of bespoke components customized to specific patient needs while preserving high levels of hygiene and material integrity.
Furthermore, the aviation industry has started to embrace this approach for its low-weight and durable elements. The capability to manufacture complex geometries with reduced scrap directly contributes to the industry's effort for optimality and environmental responsibility. By adopting rapid injection molding, aircraft manufacturers can develop faster and more efficiently, guaranteeing they meet the requirements of contemporary aviation while complying with strict safety standards.